Daifuku bietet auf die Bedürfnisse des Handels abgestimmte automatisierte Logistiklösungen. Dazu zählen sowohl energieeffizient arbeitende Lager-, Förder-, sowie Kommissionier-Techniken als auch spezielle Anwendungen für das Entladen von Containern und zum Palettieren der Containerware. „Das komplette Outsourcing von Wartung, Instandhaltung, Modernisierung und kontinuierlichen Prozessoptimierungen tritt immer häufiger an die Stelle des herkömmlichen After-sales-Service“, sagt Kurt Hager, Managing Director bei Daifuku Europe Ltd.
Im Jahr 2001 habe der Anlagenhersteller das Distributionszentrum in Køge mit einem automatisierten Palettenlager inklusive rund 17.000 Plätzen ausgestattet. Zunächst habe ein kleines Team von Aftersales-Ingenieuren die Instandhaltung übernommen, doch gestalten sich die Aufgaben heute weit umfangreicher. Inzwischen sind neben 4 Ingenieuren, die den klassischen technischen Service gewährleisten, rund ein Dutzend Mitarbeiter im Netto-Lager für den Produktionssupport zuständig. Somit sorgt in jeder Schicht ein Daifuku-Team dafür, dass sich keine Palette auf der Fördertechnik mehr festfährt und die Anlage auch sonst fehlerfrei läuft.
„Die Anzahl der Störungen, die nicht auf die Technik, sondern auf Bedienungsfehler zurückzuführen sind, wurde durch den Einsatz der Daifuku-Mitarbeiter nachhaltig gesenkt“, berichtet Jørgen Larsen, Logistics Manager bei Netto. Für den dänischen Lebensmitteldiscounter hat diese Aufgabenteilung auch den Vorteil, dass sie eine größere Flexibilität bei der eigenen Personalplanung bringt. Schließlich muss nicht mehr sichergestellt sein, dass in jeder Schicht ausreichend geschultes Personal im Einsatz ist, das die Lager- und Fördertechnik sowie die diversen Automaten bedienen kann. „Wir bezeichnen diese Art von Service als New-Age-Service: Im Mittelpunkt stehen maßgeschneiderte Konzepte und ein zentraler Ansprechpartner für alle Fragen rund um die Logistikanlage“, erläutert Hager.
Komplettes Lifecycle-Management
Mit Blick auf die technische Verfügbarkeit der Anlage ist Daifuku bei Netto für das Management des Produktlebenszyklusses verantwortlich. Für die meisten Anlagenhersteller stehe bisher im Mittelpunkt, eine Anlage möglichst kosteneffizient durch die Gewährleistungsfrist zu bringen. „Unser neues Servicekonzept ist ganzheitlicher ausgerichtet“, schildert Hager. Das äußert sich beispielsweise darin, dass sein Team täglich Reports über die Verfügbarkeit und die Leistungsfähigkeit der Anlage auswertet. Sollte ein schleichender Leistungsabfall erkennbar sein oder ein Anlagenteil mehrfach Störungen verursachen, würde das Team in Abstimmung mit Netto-Verantwortlichen Modernisierungsmaßnahmen vornehmen.
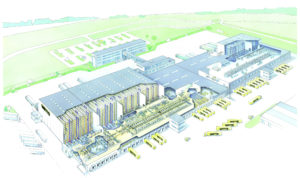
Die 3-D-Grafik des Lagers lässt bereits darauf schließen, wie übersichtlich Abläufe darin organisiert sein müssen.
Wartungen erfolgen also nicht in starren Intervallen, sondern nach Bedarf. „Weil das Team die Anlage so gut kennt, werden notwendige Wartungsarbeiten deutlich effizienter und damit für uns kostengünstiger umgesetzt“, betont Larsen. Im Laufe der Jahre sei eine Modernisierung notwendig geworden, da sich die Anzahl der unterschiedlichen Produkte seit Inbetriebnahme der Anlage fast verdreifacht hatte. Demgegenüber hatten sich die zu kommissionierenden Mengen der einzelnen Artikel stark reduziert. Der Trend zur immer größeren Vielfalt von Produkten in Supermarktregalen und immer geringeren Mengen pro Artikel, die entsprechend bevorratet werden, ist nach wie vor ungebrochen. Doch die Kapazität des Netto-Lagers hatte seine Grenzen erreicht – statt des angestrebten Zweischichtbetriebs wurde mittlerweile an sieben Tagen pro Woche im Dreischichtbetrieb gearbeitet.
Umsetzung in sehr kleinen Zeitfenstern
Eine Herausforderung bei der Modernisierung waren die kleinen Zeitfenster, die für den Umbau der Lagertechnik zur Verfügung standen. Die oberste Priorität lautete, dass der laufende Betrieb in keiner Weise gestört werden durfte. Somit blieb das Lager mit 23 Gassen, der Kommissionieranlage mit Kippschalensorter, drei automatischen und zwei manuellen Packbereichen sowie einer Versand- /Pufferanlage mit Sorting Transfer Vehicle (STV) in der Funktion erhalten. Durch die Modifikation von acht Gassen für die Zwischenlagerung von vorkommissionierten Kundenpaletten wurde es jedoch optimiert. Zum Beispiel ließ sich der Durchsatz der Auslagerstationen erhöhen, wodurch sich Wartezeiten bei der manuellen Kommissionierung reduzierten. „Insgesamt wurde die Anlage spürbar entlastet, sodass wieder angemessene Zeitfenster für Wartungsarbeiten und Systempflege zur Verfügung stehen“, bekräftigt Larsen.
Das Konzept, das auf einer wirtschaftlichen Nutzenanalyse von Daifuku – genannt „Quick StudyTM“ – basiert, beinhaltete auch die Errichtung eines automatischen Hochregallagers mit acht Gassen und mehr als 6.000 Palettenplätzen auf 2.080 qm für haltbare Lebensmittel, Wein und Spirituosen sowie Non-Food-Artikel. Hier kommen acht Regalbediengeräte zum Einsatz, der neue Lagerbereich wird als Pre-Pack-Lager mit Versandpuffer-Funktion genutzt. Vor der Modernisierung reichten die vorhandenen Versandbahnen aufgrund der stark gestiegenen Warenmengen für die Bereitstellung zum Versand kaum aus. So kam es bei der Beladung von LKWs immer wieder zu Wartezeiten. „Der neue Versandpuffer schafft hier Abhilfe“, freut sich Larsen.
Um die Prozesse in den Lagerbereichen miteinander zu verzahnen, erweiterte Daifuku einen Kippschalensorter um 28 zusätzliche Zielstellen mit jeweils einem Packplatz. Darüber hinaus schuf Daifuku einen „Bypass“ aus herkömmlicher Fördertechnik. Aufgrund der hohen Auslastung des Systems musste der Umbau des Sorters im laufenden Betrieb innerhalb von einem Wochenende realisiert werden. Ein ebenso enger Zeitrahmen galt für die Anbindung der acht neuen Lagergassen an den STV-Loop in der Lagervorzone.
Aufgrund der hohen Fahrgeschwindigkeiten der schienengeführten Fahrzeuge und der Optimierung des Materialflusses kann der Loop weiter mit derselben Anzahl von Fahrzeugen betrieben werden. Zudem integrierte das Daifuku-Team einen Sonderkommissionierbereich mit automatischer Bereitstellung für Viertelpaletten, die zuvor nur manuell abgefertigt werden konnten. So kommen im Lager jetzt ergonomische Handhabungsgeräte, 24 Gefällerollbahnen, ein automatischer Folienwickler sowie ein automatisches Palettenprüfsystem zum Einsatz. Das Ergebnis: „Seit der Modernisierung können wir wieder wie gewünscht im Zweischichtbetrieb arbeiten“, stellt Larsen fest.
Foto und Grafik: Rabea Schalow/Additiv PR GmbH
Weitere Informationen: www.netto.de und www.daifukueurope.com