Runners Point, Recklinghausen, einer der führenden deutschen Filialfachhändler im Bereich Sportschuhe, Funktionstextilien und Zubehör, hat durch eine Umstellung seiner internen Logistik-Organisation spürbare und nachhaltige Einsparungen erzielt. Im Kern handelt es sich bei den Maßnahmen um eine Rückverlagerung von Verantwortlichkeiten und Funktionalitäten von den Filiallagern auf das Zentrallager. Eine wichtige Rolle spielt dabei die Unterstützung durch eine moderne IT-Lösung.
Das Unternehmen betrieb zum Zeitpunkt der Neustrukturierung im vergangenen Jahr 160 Filialen in Deutschland, den Niederlanden und Österreich. In einem Zentrallager mit 8.500 qm Lagerfläche wurden durchschnittlich 450.000 Teile bevorratet. Von hier aus wurden im vergangenen Jahr 145.000 Pakete versendet. „Wir hatten teilweise einen recht hohen Lagerbestand in den Filialen und entsprechend geringe Bestände im Zentrallager“, sagt Thomas Brokop, Leiter Organisation/IT bei Runners Point.
Hinzu kam eine hohe Zahl an Filialquerverschiebungen (Umlagerungen), wenn die jeweilige Ware nicht mehr im Zentrallager vorhanden und auch auf Lieferantenseite nicht mehr verfügbar war. „Insgesamt kamen wir auf 12.000 Filialumlagerungen pro Monat“, so Brokop. Das Problem waren Versandkosten und manueller Aufwand, die mit dem Verpacken von Kleinstmengen in den Filialen und dem Versand in eine andere Filiale verbunden waren. „Oft wussten die Filialleiter auch nicht, wohin mit den vielen Einzelpaketen, die sie aus vielen verschiedenen Filialen gleichzeitig erhielten.“
Beeindruckende Bilanz
Zielsetzung für eine Neustrukturierung der Supply Chain war aus diesen Gründen eine optimierte Nachversorgung aus dem Zentrallager und eine Verringerung des Aufwands für die Filialen. Diese sogenannte zentralseitige Nachversorgung basiert zum einen auf einer täglichen Überprüfung der Nachlieferfähigkeit eines jeden Einzelartikels durch den jeweiligen Lieferanten. Kann dieser nicht mehr liefern oder das Zentrallager nicht mehr zeitnah versorgen, werden Schnelldreher aus den Beständen von Filialen mit hohen Beständen zurück an das Zentrallager geschickt.
Bei diesen Artikeln handelt es sich um Produkte, von denen zuvor bis zu vier Stück je Einzelartikel in den Filialen bevorratet wurden. Mit der Neuorganisation konnten diese Bestände halbiert werden. „Das reicht aus, weil sich diese Artikel aufgrund von Erfahrungswerten nur zweimal pro Woche verkaufen“, erklärt Brokop. „Durch unsere tägliche Nachbelieferung der Filialen ist dann trotzdem ausreichend Bestand vorhanden.“ Erleichtert wird diese Vorgehensweise dadurch, dass ein Kunde im Falle von Sortimentslücken sich die Ware auch nach Hause schicken lassen oder aber nach erneutem Wareneingang in der Filiale abholen kann.
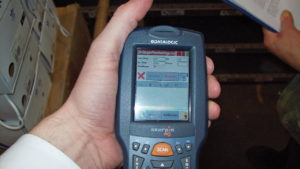
Übersenden der Lagerdaten an Lagerverwaltungssystem und Warenwirtschaft: Damit ist der Artikel wieder kommissionierfähig.
Beim Eintreffen der Ware, die ans Zentrallager zurückgeschickt wurde, wird der Lieferschein mit einem mobilen Datenerfassungsgerät eingescannt, ebenso die Artikelnummer der Einzelartikel und der Barcode des Lagerfachs. In jedem der 1.900 Lagerfächer wird nur ein Artikel, also beispielsweise ein Paar Laufschuhe, gelagert. Damit ist eine eindeutige Identifizierung und Ortung auf Einzelartikelebene möglich.
Die Informationen des Eingangs der Ware aus einer Filiale im Zentrallager werden vom MDE an das Lagerverwaltungssystem und die Warenwirtschaft übermittelt. Damit stehen die eingelagerten Artikel erneut bereit zur Kommissionierung. Lieferscheinkontrolle und alle Buchungen finden automatisiert statt.
Notwendig war dafür ein neues Software-Modul. Das Modul wurde vom IT-Anbieter Futura Retail Solution (Stelle/Hamburg) entwickelt. Entscheidend für eine Optimierung der Lieferkette war außerdem eine Neujustierung der Zeiträume, für die das Warenwirtschaftssystem „FuturERS“ schon vor der Neuorganisation Prognosen erstellte. Der Zeitraum der Prognosen konnte von zehn auf fünf Tage verkürzt werden. Denn die optimierte tägliche Nachlieferung mit Sortiments-„Rennern“ erlaubt jetzt geringere Mindestbestände in den Filialen.
Geringere Mindestbestände
„Die Lösung errechnet auf der Basis von Abverkaufsdaten unterschiedlich langer Perioden die benötigte Soll-Menge. Dabei werden Lagerbestände und Lieferzeiten der Lieferanten berücksichtigt. Die daraus abgeleiteten Prognosen verhindern sowohl Überbestände als auch Engpässe“, sagt Futura-Vorstand Vanjo Wandscher. Das System verfügt zudem über Werkzeuge für automatisierte Umlagerungs-
vorschläge.
Eine erste Zwischenbilanz zu Jahresbeginn zeigte eine positive Entwicklung: Im Januar 2011 lag die Zahl der Filialumlagerungen um 3.800 respektive 31 Prozent niedriger als im Vergleichsmonat des Vorjahres, und die Versandkosten konnten um zwölf Prozent reduziert werden – dies alles bei einer um neun Prozent erhöhten Filialzahl und eines um 16 Prozent höheren Umsatzes.
Laut Thomas Brokop konkretisiert sich der Nutzen für die einzelnen Filialen an folgenden Punkten: Reduzierung der Anzahl der zu packenden Pakete, vereinfachtes Lagermanagement durch Reduzierung des Warenvolumens, kaum Sortimentslücken, signifikante Reduzierung von Abschriften für die Vermarktung von Einzelpaaren. „Der Kunde findet damit so gut wie immer seinen Wunschartikel vor, und unsere Mitarbeiter haben mehr Zeit für das Beratungsgespräch“, ist Brokop überzeugt.
Entscheidend ist, wie man es organisiert
Runners Point hat die Logistik in die Filialen komplett neu aufgestellt. Fragen an Thomas Brokop, Leiter Organisation/IT:
Auf den ersten Blick wirkt die neue Lösung komplexer als die bisherige. Stimmt das?
BROKOP: Nein, ist sie nicht. Viele Unternehmen scheuen den Rückversand von Ware aus den Filialen an das Zentrallager und den damit verbundenen Aufwand der sorten- und größenreinen Sortierung und Lagerung, der Identifizierung und Verfolgung der Einzelartikel. Entscheidend ist aber, wie dieser Warenfluss organisiert ist.
Was bedeutet das konkret?
BROKOP: Wir vermeiden großen Aufwand, weil wir zum einen vieles automatisiert haben und uns zum anderen bei dieser Vorgehensweise auf die wichtigen, schnelldrehenden Artikel beschränken. Automatisierung ermöglichen wir dadurch, dass jeder Einzelartikel in einem Lagerfach mit fixer Codierung gelagert wird. Das IT-System weiß, wo sich der Artikel befindet. Ein manuelles Zählen oder Sortieren der Ware entfällt.
Wie geschieht das Kommissionieren vor dem Versand in die Filialen?
BROKOP: Hier arbeiten wir mit ganz normalen Mechanismen. Das Lagerverwaltungssystem erstellt eine Pick-Liste und gibt dem Lagermitarbeiter die optimale Wegeführung vor. Dabei wird das Regal mit den Filialrücksendungen immer zuerst angesteuert. Sobald das Fach leer ist, kann es erneut für Ware benutzt werden, die aus einer Filiale zurückgesendet wurde.
Filialist und Franchise-Geber
Runners Point wurde 1984 als Tochter des damaligen Karstadt Quelle-Konzerns gegründet. Der Filialist hat ein starkes Standbein im Laufschuh-Markt. Seit 2005 ist die Hannover Finanz Gruppe Haupteigentümer des Unternehmens. Aktuell werden vom Stammsitz in Recklinghausen 165 Filialen (darunter auch die Formate Sidestep und Run2) in Deutschland, Österreich und den Niederlanden gesteuert und zentral beliefert. Runners Point beschäftigt rund 1.600 Mitarbeiter. Neben den eigenen Filialen hat Runners Point ein Franchise-System etabliert.